What Will It Take for Electric Vehicles to Create Jobs, Not Cut Them?
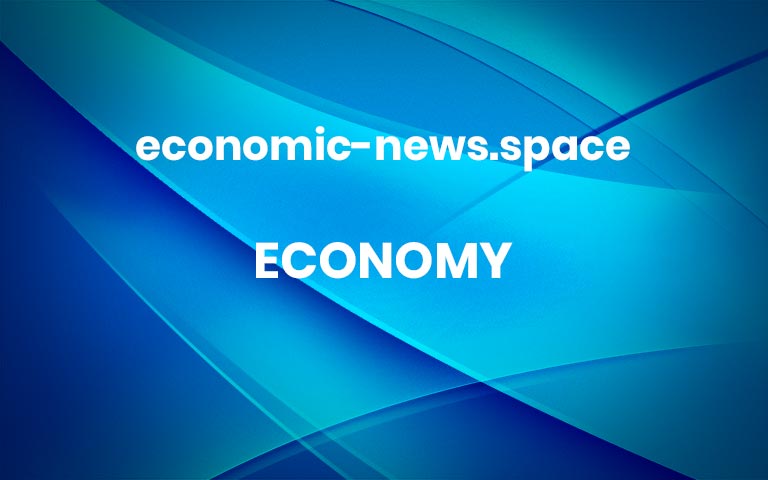
A report by a liberal think tank tries to quantify the potential employment gains and losses, concluding that subsidies will be crucial.When President Biden announced his multitrillion-dollar jobs plan in March, it included nearly $175 billion in spending to encourage Americans to buy electric vehicles.The money would help ensure “that these vehicles are affordable for all families and manufactured by workers with good jobs,” the White House wrote at the time.Now, as Mr. Biden’s plan wends its way through Congress, a liberal think tank has tried to flesh out the number of jobs to be gained or lost in the transition away from internal-combustion vehicles.The report, released Wednesday by the Economic Policy Institute, concluded that it would take government subsidies focused on developing a domestic supply chain and increasing demand for U.S.-made vehicles to avoid job losses.It found that without additional government investment, the industry could lose about 75,000 jobs by 2030, the year by which Mr. Biden wants half the new vehicles sold in the country to be electric.By contrast, the report said, if government subsidies were targeted to increase the portion of electric vehicle components that are manufactured domestically, and to increase the market share of U.S.-made vehicles, the industry could add about 150,000 jobs by the end of the decade.“That’s the payoff — making the sector a center of good jobs again,” said Josh Bivens, an economist who is one of the report’s authors. “If we don’t try to react proactively with good policy we’ll see continued downward pressure on the number of good jobs.”Looming over the transition to electric vehicles is the fact that they have substantially fewer moving parts than gasoline-powered ones and require less labor to manufacture — about 30 percent less, according to figures from Ford Motor. The vehicle-manufacturing industry employs a little under one million people domestically, including suppliers.The cab of an all-electric Ford F-150 Lightning truck prototype. Ford and General Motors have said they are taking on a greater role in battery production.Rebecca Cook/ReutersThere are essentially two ways to offset the projected job losses: to increase the proportion of each vehicle’s parts that are made domestically — specifically in the powertrain, the key parts and systems that power a car — and to sell more vehicles assembled in the United States.Mr. Bivens and his co-author, James Barrett, an economic consultant, examine the effects of doing both. They note that roughly three-quarters of the parts in the powertrain for a U.S.-made gasoline vehicle are produced domestically, versus less than half of the parts in the powertrain of a U.S.-made electric vehicle.Raising the proportion of domestic content in electric vehicles so that it mirrors gas-powered ones could save tens of thousands of jobs a year, they estimate — potentially more than half the likely job losses that would arise without additional government action.But to transform likely job deficits into job gains, Mr. Barrett and Mr. Bivens find, it is necessary to increase the market share of vehicles made in the United States. According to the study, the percentage of vehicles sold in the United States that are made domestically has hovered around 50 percent over the past decade. If it were to rise to 60 percent, the authors conclude, the industry could gain over 100,000 jobs in 2030.If market share were instead to drop to 40 percent by the end of the decade and there were no increase in the domestic content of electric vehicle powertrains, the industry could lose more than 200,000 jobs, the report finds.Under the Democratic plan circulating in Congress, a current $7,500 tax credit for the purchase of a new electric vehicle would rise as high as $12,500. An extra $4,500 would apply to vehicles assembled at unionized factories in the United States. Consumers would receive the final $500 if their vehicle had a U.S.-made battery. The details could change in the face of opposition from automakers with nonunion U.S. plants.Democrats are also discussing subsidies to encourage manufacturers to set up new factories or upgrade old ones.Sam Abuelsamid, an auto industry analyst at Guidehouse Insights, said that domestic automakers had an opportunity to increase market share as the industry electrifies and that an expanded consumer tax credit would help.“They are targeting a lot of the market segments that are particularly strong-selling — crossovers, pickups,” Mr. Abuelsamid said. “There is definitely potential for them to claw back some market share from Asian brands.”Still, he warned, the window for seizing the opportunity could be relatively narrow as Asian automakers like Toyota and Honda, which have lagged somewhat in their electric vehicle planning, introduce more electric offerings.The question of whether manufacturers will locate production of electric vehicles and their components in the United States as demand grows, and the extent to which government subsidies can help ensure that this happens, has been a subject of debate in recent years.Dale Hall, a researcher at the International Council on Clean Transportation, a research organization, said in an interview that electric vehicles tend to be manufactured in the region where they are sold, both to save on transportation costs and to be more responsive to consumers’ needs. More