Russia Sidesteps Western Punishments, With Help From Friends
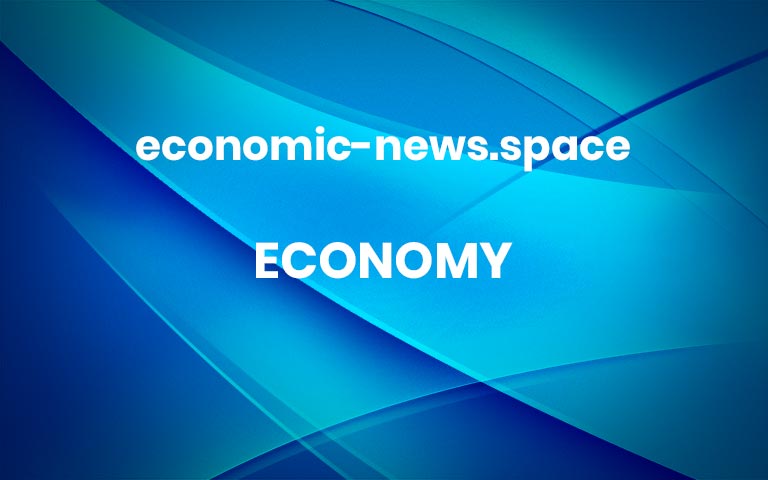
A surge in trade by Russia’s neighbors and allies hints at one reason its economy remains so resilient after sweeping sanctions.WASHINGTON — A strange thing happened with smartphones in Armenia last summer.Shipments from other parts of the world into the tiny former Soviet republic began to balloon to more than 10 times the value of phone imports in previous months. At the same time, Armenia recorded an explosion in its exports of smartphones to a beleaguered ally: Russia.The trend, which was repeated for washing machines, computer chips and other products in a handful of other Asian countries last year, provides evidence of some of the new lifelines that are keeping the Russian economy afloat. Recent data show surges in trade for some of Russia’s neighbors and allies, suggesting that countries like Turkey, China, Belarus, Kazakhstan and Kyrgyzstan are stepping in to provide Russia with many of the products that Western countries have tried to cut off as punishment for Moscow’s invasion of Ukraine.Those sanctions — which include restrictions on Russia’s largest banks along with limits on the sale of technology that its military could use — are blocking access to a variety of products. Reports regularly filter out of Russia about consumers frustrated by high-priced or shoddy goods, ranging from milk and household appliances to computer software and medication, said Maria Snegovaya, a senior fellow for Russia and Eurasia at the Center for Strategic and International Studies, in an event at the think tank this month.Even so, Russian trade appears to have largely bounced back to where it was before the invasion of Ukraine last February. Analysts estimate that Russia’s imports may have already recovered to prewar levels, or will soon do so, depending on their models.In part, that could be because many nations have found Russia hard to quit. Recent research showed that fewer than 9 percent of companies based in the European Union and Group of 7 nations had divested one of their Russian subsidiaries. And maritime tracking firms have seen a surge in activity by shipping fleets that may be helping Russia to export its energy, apparently bypassing Western restrictions on those sales.While Western countries have not banned the shipment of consumer products like cellphones and washing machines to Russia, other sweeping penalties were expected to clamp down on its economy. They include a cap on the price that Russia can charge for its oil as well as restricted access to semiconductors and other critical technology.Companies like H&M halted operations in Russia after the invasion of Ukraine, but the economy has proved resilient.Maxim Shipenkov/EPA, via ShutterstockSome companies, including H&M, IBM, Volkswagen and Maersk, halted operations in Russia after the invasion, citing moral and logistical reasons. But the Russian economy has proved surprisingly resilient, raising questions about the efficacy of the West’s sanctions. Countries have had difficulty reducing their reliance on Russia for energy and other basic commodities, and the Russian central bank has managed to prop up the value of the ruble and keep financial markets stable.On Monday, the International Monetary Fund said it now expected the Russian economy to grow 0.3 percent this year, a sharp improvement from its previous estimate of a 2.3 percent contraction.The I.M.F. also said it expected Russian crude oil export volume to stay relatively strong under the current price cap, and Russian trade to continue being redirected to countries that had not imposed sanctions.Most container ships have stopped ferrying goods like phones, washing machines and car parts into the port of St. Petersburg. Instead, such products are being carried on trucks or trains from Belarus, China and Kazakhstan. Fesco, the Russian transport operator, has added new ships and new ports of call to a route with Turkey that transports Russian industrial goods and foreign appliances and electronics between Novorossiysk and Istanbul.Sergey Aleksashenko, former deputy minister of finance of the Russian Federation, said at an event this month that 2023 would be “a difficult year” for the Russian economy, but that there would be “no catastrophe, no collapse.”Some parts of the Russian economy are struggling, he said, pointing to car factories that shut down after being unable to secure parts from Germany, France, Japan and South Korea. But military expenditures and higher energy prices helped prop it up last year.“We may not say that Russian economy is in tatters, that it is destroyed, that Putin lacks funds to continue his war,” Mr. Aleksashenko said, referring to President Vladimir V. Putin. “No, it’s not true.”Russia stopped publishing trade data after its invasion of Ukraine. But analysts and economists can still draw conclusions about its trade patterns by adding up the commerce that other countries report with Russia.The International Monetary Fund said it expected Russian crude oil exports to stay relatively strong despite a Western price cap. Andrey Rudakov/BloombergMatthew Klein, an economics writer and a co-author of “Trade Wars Are Class Wars,” is one of the people drawing conclusions about this Russia-size hole in the global economy. According to his calculations, the value of global exports to Russia in November was just 15 percent below a monthly preinvasion average.Global exports to Russia most likely fully recovered in December, though many countries have not yet issued their trade data for the month, he said.“Most of that recovery has been driven overall by China and Turkey particularly,” Mr. Klein said.It’s unclear how much of this trade violates sanctions imposed by the United States and Europe, but the patterns are “suspicious,” he said. “It would be consistent with the idea that there are ways of trying to get around some of the sanctions.”Silverado Policy Accelerator, a Washington nonprofit, recently issued a similar analysis, estimating that the value of Russian imports from the rest of the world had exceeded prewar levels by September.One of the case studies in that report was the jump in Armenian smartphone sales. Andrew S. David, the senior director of research and analysis at Silverado, said the trends reflected how supply chains had shifted to continue providing Russia with goods.Samsung and Apple, previously major suppliers of Russian cellphones, pulled out of the Russian market after the invasion. Exports of popular Chinese phone brands, like Xiaomi, Realme and Honor, also initially dipped as companies struggled to understand and cope with new restrictions on sending technology or making international payments to Russia.But after an “adjustment period,” Chinese brands started to take off in Russia, Mr. David said. Overall Chinese exports to Russia reached a record high in December, helping to offset a steep drop in trade with Europe. Apple and Samsung phones also appeared to begin to find their way back to Russia, rerouted through friendly neighboring countries.“Armenia is certainly not the only one,” Mr. David said. “There’s a lot coming through central western Asia, Turkey and the former Soviet republics.”Shipments to Russia of other products, like passenger vehicles, have also rebounded. And China has increased exports of semiconductors to Russia, though Russia’s total chip imports remain below prewar levels.President Vladimir V. Putin at a military training facility in Russia. Military expenditures and higher energy prices helped prop up the Russian economy last year.Pool photo by Mikhail KlimentyevOne major open question is how effectively the Western price cap will hold down Russia’s oil revenue this year.The cap allows Russia to sell its oil globally using Western maritime insurance and financing as long as the price does not exceed $60 per barrel. That limit, which is essentially an exception to Group of 7 sanctions, is designed to keep oil flowing on global markets while limiting the Russian government’s revenue from it.Some analysts have suggested that Russia is finding ways around the effort by using ships that do not rely on Western insurance or financing.Ami Daniel, the chief executive of Windward, a maritime data company, said he had seen hundreds of instances in which people from countries like the United Arab Emirates, India, China, Pakistan, Indonesia and Malaysia bought vessels to try to set up what appeared to be a non-Western trading framework for Russia.“Basically, Russia has been gearing up toward being able to trade outside of the rule of law,” he said.Mr. Daniel said his firm had also seen a sharp uptick in shipping practices that appeared to be Russian efforts to contravene Western sanctions. They include transfers of Russian oil between ships far out at sea, in international waters that are not under the jurisdiction of any country’s navy, and attempts by ships to mask their activities by turning off satellite trackers that log their location or transmitting fake coordinates.Much of this activity had been taking place in the mid-Atlantic Ocean. But after media coverage of suspicious practices in this region, the hub moved south, off the coast of West Africa, Mr. Daniel said.“They’re exploding,” he said of deceptive shipping practices. “It’s happening at an industrial scale.”So far, the oil price cap appears to be accomplishing its goal of reducing the price that Russia can charge while keeping global supplies flowing. But it remains to be seen whether this shadow fleet of ships is big enough to allow Russia to buy and sell oil outside the cap, said Ben Cahill, a senior fellow at the Center for Strategic and International Studies, during a January panel discussion.“If that fleet is big enough for Russia to really operate outside the reach” of the Group of 7 countries, the cap probably “won’t have the kind of leverage that policymakers wanted,” Mr. Cahill said. “I think we should know within a couple of months.”Alan Rappeport More