Warehouses Transform N.Y.C. Neighborhoods as E-Commerce Booms
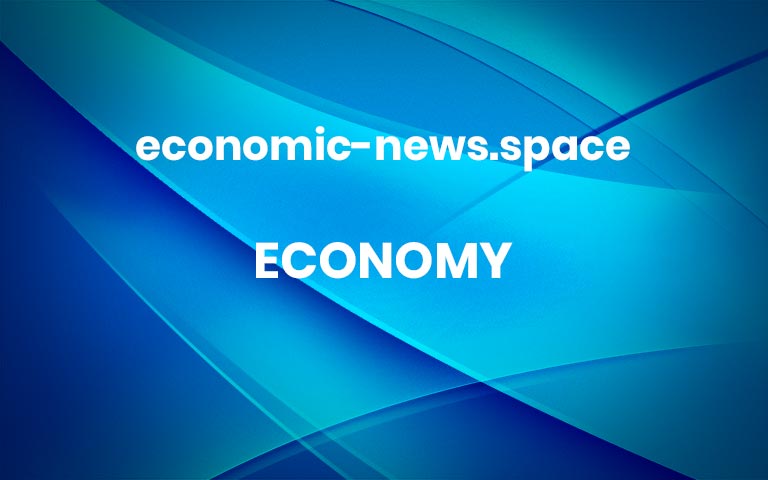
The region is home to the largest concentration of online shoppers in the country. The facilities, key to delivering packages on time, are reshaping neighborhoods.An e-commerce boom turbocharged by the pandemic is turning the New York City region into a national warehouse capital.In just two years, Amazon has acquired more than 50 warehouses across the city and its surrounding suburbs. UPS is building a logistics facility larger than Madison Square Garden on the New Jersey waterfront near Lower Manhattan.In Brooklyn, Queens and the Bronx, 14 huge warehouses to help facilitate e-commerce operations are rising, including multistory centers previously found only in Asia.Fueled by the soaring growth of e-commerce while so many Americans have been working from home, online retailers, manufacturers and delivery companies are racing to secure warehouses in the country’s most competitive real estate market for them.Every day, more than 2.4 million packages are delivered just in New York City, an online-buying mecca in a region of 20.1 million people.The feverish activity has already transformed the landscape of city neighborhoods and rural towns, transforming Red Hook in Brooklyn into a bustling logistics hub and replacing farmland in southern New Jersey with sprawling warehouses where packages are sorted, packed and delivered, often within hours of being ordered.An Amazon grocery hub in Red Hook, Brooklyn, which has emerged as a nexus of e-commerce warehouses in New York because it offers relatively easy access to Lower Manhattan, Queens and the rest of Brooklyn.Clark Hodgin for The New York TimesJust 1.6 percent of all warehouses in New York City and only 1.3 percent in New Jersey are available for lease, according to the real estate firm JLL; only the Los Angeles area has fewer warehouse vacancies in the United States. Some companies are converting buildings never intended to be warehouses. Amazon turned a shuttered supermarket in Queens into a makeshift package hub.The soaring demand for warehouses, once the ugly duckling of the real estate industry, underscores their pivotal role in a complex global supply chain. Nationwide, developers are pouring billions of dollars into the construction of new facilities, helping lift the commercial real estate sector, which has been battered by the emptying of offices during the pandemic.But the rise of warehouses has also sparked significant opposition. While they provide jobs and can lower residential property taxes by contributing to the local tax base, people across the region say the large hubs will lead to constant flows of semi-trucks and delivery vans that will worsen pollution and traffic congestion.Understand the Supply Chain CrisisThe Origins of the Crisis: The pandemic created worldwide economic turmoil. We broke down how it happened.Explaining the Shortages: Why is this happening? When will it end? Here are some answers to your questions.A New Normal?: The chaos at ports, warehouses and retailers will probably persist through 2022, and perhaps even longer.A Key Factor in Inflation: In the U.S., inflation is hitting its highest level in decades. Supply chain issues play a big role.They have also bemoaned the loss of open land to mega facilities. In recent months, residents in the southern New Jersey township of Pilesgrove, just across the Delaware River from Wilmington, Del., protested plans for a 1.6 million square-foot warehouse — larger than Ellis Island — on former farmland.While Amazon, major retailers and logistics operators such as UPS, FedEx and DHL dominated the initial wave of warehouse deals at the start of the pandemic, interest is now coming from smaller businesses seeking greater control of their supply chain amid a global bottleneck in the movement of goods.“I’ve been doing this for 30-some-odd years, and I’ve never seen it like this,” said Rob Kossar, a vice chairman at JLL who oversees the company’s industrial division in the Northeast. “In order for tenants to secure space, they are having to negotiate leases with multiple landlords on spaces that aren’t even available. It’s insane what they are having to do.”The rising cost to lease facilities has frustrated some small business owners who cannot compete with retail and logistics giants, as well as newcomers like Tesla and Rivian, which have opened showrooms and service centers for their electric vehicles in Brooklyn warehouses. Leasing prices for warehouses in the Bronx, for instance, have jumped 22 percent since the pandemic started.Warehouse jobs are still just a fraction of New York City’s labor force, but companies are on a hiring spree. Since 2019, the number of warehouse jobs doubled to 16,500 positions in late 2021. New hires at Amazon make around $18 an hour and get starting bonuses up to $3,000. But the company has also been fighting workers at some of its warehouses, including on Staten Island, who are trying to unionize to improve working conditions.Prose employs about 150 employees at its facility in Brooklyn from where it ships products across the United States and to Canada.Clark Hodgin for The New York TimesToday, nearly everything — from cars to electronics and groceries to prescription drugs — can be ordered online and arrive in as little as a few hours. In New York City, new companies are offering 15-minute grocery delivery.And though most retail sales nationwide still happen at brick-and-mortar stores, online sales are increasing at breakneck speed, growing by 50 percent over the last five years to reach 13 percent of all retail purchases, according to the census.That surge is pummeling many retailers, especially smaller businesses, that have also had to weather the loss of customers during the pandemic.At the onset of the pandemic shoppers switched to online buying at a rate that had been expected to take a decade to reach, according to analysts.Some large retailers, such as Target and Best Buy, that have a handful of warehouses in the region lean on their stores to fulfill online orders. Wal-Mart, the nation’s largest retailer, does not have a store in New York City so it uses a warehouse in Lehigh Valley, Pa., just over the border from New Jersey, and stores in surrounding suburbs to serve city residents.Amazon is taking a different approach. Across New Jersey to the northern New York City suburbs to Long Island, Amazon is cobbling together a sprawling network of fulfillment centers, package-sorting facilities and last-mile hubs. In the city it has set up a handful of facilities in the Red Hook and Sunset Park neighborhoods of Brooklyn.Amazon’s rapid expansion is not unique to the New York area. Last September alone, Amazon said in a recent earnings call, it added another 100 facilities to its delivery network in the United States.Red Hook, a neighborhood of just under a square mile bounded by water on three sides, has become a center for warehouses in the city because it is near major roadways into population centers in other parts of Brooklyn, Lower Manhattan and Queens.The owner of Prose decided to keep all his manufacturing under one roof before the supply chain problems emerged. “It has been a great decision,” he said.Clark Hodgin for The New York TimesAt least three new warehouses have opened in the neighborhood and more could be on the horizon. UPS paid $300 million for a 12-acre property, and two developers of logistics centers spent $123 million in December to buy several industrial sites there.How the Supply Chain Crisis UnfoldedCard 1 of 9The pandemic sparked the problem. More