Supply-Chain Kinks Force Small Manufacturers to Scramble
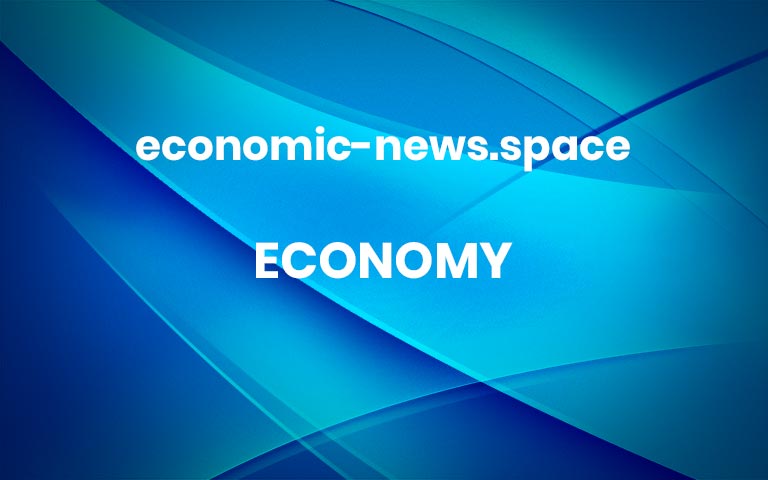
Facing delays, shortages and higher prices for raw materials, small manufacturers are finding new sources. Not all are able to pass along the costs.Peak season has arrived for DPS Skis, a manufacturer and distributor of mountain sports gear in Salt Lake City. But this year, the winter challenges began far from the slopes.A kinked-up global supply chain has forced Alex Adema, the chief executive, to find new sources for the wood used in his company’s skis and to get crucial items like bindings and poles.“The window is really short,” he said. “Skiers get excited when they know snow is coming.”Facing long delays in getting finished goods and raw material from Asia and Europe because of a lack of freighter space and overloaded ports, small to medium-size manufacturers like DPS are being forced to adapt quickly.Unlike giants such as Walmart, they lack the means to charter their own cargo ships — or to design their own semiconductors, as Ford Motor said it would do this month. Instead, they are revisiting some of the practices — lean inventories, just-in-time deliveries, and reliance on components from China and other faraway suppliers — that were part of the established factory playbook.“The more control you have over your own supply chain, the better,” said Scott Paul, president of the Alliance for American Manufacturing, a policy group representing manufacturers and the United Steelworkers.In practice, that means meeting needs through less-distant sources. “That way,” Mr. Paul said, “you’re either first in line or have a leg up.” But that can push up costs — a burden that is sometimes passed along to customers, and in other cases is absorbed by the businesses.Until this year, DPS bought the Paulownia species of hardwood for the core of many of its skis from China, but shipping delays meant that running out of the material was a real possibility. At one point as supplies dwindled in October, “we were holding our breath,” Mr. Adema said.DPS found a supplier of Paulownia in North Carolina, and after much testing, the specifications matched up. “You can’t just swap species,” Mr. Adema said. “We’re excited about getting the wood from North Carolina in terms of sustainability and less environmental imprint. Any time you can throw something on a train in the U.S., it’s better than a ship or plane.”Not everything is available domestically, however. Ski poles and ski bindings still come from Europe, and DPS has been forced to resort to airfreight to bring in supplies of these items, even though it’s four times as expensive as shipping by sea.And while DPS ships by boat whenever possible, it’s hardly cheap — the price of shipping a container has gone from roughly $5,000 to $20,000 in some cases, Mr. Adema said. Overall, raw material costs for DPS are up 10 to 15 percent..css-1xzcza9{list-style-type:disc;padding-inline-start:1em;}.css-3btd0c{font-family:nyt-franklin,helvetica,arial,sans-serif;font-size:1rem;line-height:1.375rem;color:#333;margin-bottom:0.78125rem;}@media (min-width:740px){.css-3btd0c{font-size:1.0625rem;line-height:1.5rem;margin-bottom:0.9375rem;}}.css-3btd0c strong{font-weight:600;}.css-3btd0c em{font-style:italic;}.css-1kpebx{margin:0 auto;font-family:nyt-franklin,helvetica,arial,sans-serif;font-weight:700;font-size:1.125rem;line-height:1.3125rem;color:#121212;}#NYT_BELOW_MAIN_CONTENT_REGION .css-1kpebx{font-family:nyt-cheltenham,georgia,’times new roman’,times,serif;font-weight:700;font-size:1.375rem;line-height:1.625rem;}@media (min-width:740px){#NYT_BELOW_MAIN_CONTENT_REGION .css-1kpebx{font-size:1.6875rem;line-height:1.875rem;}}@media (min-width:740px){.css-1kpebx{font-size:1.25rem;line-height:1.4375rem;}}.css-1gtxqqv{margin-bottom:0;}.css-19zsuqr{display:block;margin-bottom:0.9375rem;}.css-12vbvwq{background-color:white;border:1px solid #e2e2e2;width:calc(100% – 40px);max-width:600px;margin:1.5rem auto 1.9rem;padding:15px;box-sizing:border-box;}@media (min-width:740px){.css-12vbvwq{padding:20px;width:100%;}}.css-12vbvwq:focus{outline:1px solid #e2e2e2;}#NYT_BELOW_MAIN_CONTENT_REGION .css-12vbvwq{border:none;padding:10px 0 0;border-top:2px solid #121212;}.css-12vbvwq[data-truncated] .css-rdoyk0{-webkit-transform:rotate(0deg);-ms-transform:rotate(0deg);transform:rotate(0deg);}.css-12vbvwq[data-truncated] .css-eb027h{max-height:300px;overflow:hidden;-webkit-transition:none;transition:none;}.css-12vbvwq[data-truncated] .css-5gimkt:after{content:’See more’;}.css-12vbvwq[data-truncated] .css-6mllg9{opacity:1;}.css-qjk116{margin:0 auto;overflow:hidden;}.css-qjk116 strong{font-weight:700;}.css-qjk116 em{font-style:italic;}.css-qjk116 a{color:#326891;-webkit-text-decoration:underline;text-decoration:underline;text-underline-offset:1px;-webkit-text-decoration-thickness:1px;text-decoration-thickness:1px;-webkit-text-decoration-color:#326891;text-decoration-color:#326891;}.css-qjk116 a:visited{color:#326891;-webkit-text-decoration-color:#326891;text-decoration-color:#326891;}.css-qjk116 a:hover{-webkit-text-decoration:none;text-decoration:none;}These kind of increases are coursing through the economy, and are a primary reason inflation is running at the fastest pace in 31 years, with a 6.2 percent increase in prices in October from a year earlier. But unlike many other companies, DPS hasn’t been able to pass on the higher costs to consumers.“Our ski shop customers place their orders in the spring, and they’ve committed to pricing and delivery dates for this upcoming season,” Mr. Adema said. Designed for backcountry touring as well as resort trails, the company’s skis sell for about $800 to $1,400 a pair. Poles begin at $99. “For us to change prices in midstream would not be good for relations with our community,” Mr. Adema added. “We have to absorb the costs.”Other manufacturers face many of the same issues but have more flexibility on prices. Honey-Can-Do, a maker of housewares like storage carts and shelving in Chicago, has been able to pass along its higher costs, said Steve Greenspon, the company’s owner and chief executive.“Everybody knows what’s going on,” Mr. Greenspon said. “It’s become commonplace and accepted this year for retailers to accept cost increases. I’ve heard from merchants that over 90 percent of vendors are giving them price increases.”This trend marks a turnabout from prepandemic days. “If you tried to pass along a major price increase to a big retailer a couple of years ago, there’d be concerns about your relationship,” Mr. Greenspon said. “But in the current atmosphere, it’s the norm.”Honey-Can-Do’s prices are up roughly 10 percent to 25 percent, depending on the raw materials, freight costs and how much corrugated packaging is used in shipping. Its products include a 65-inch baker’s rack with a cutting board and hanging storage that retails for $119.99 and a toy organizer with 12 bins that sells for $59.99.The company has streamlined its product offerings, narrowing the focus to its top sellers. “We don’t want to use up our container capacity with slower-moving items,” Mr. Greenspon said. “We want to use that space for high-velocity items.”“Instead of multiple colors and many variations, companies are making things more neutral,” he added. “We’re focusing on proven winners.”The company is also increasing the inventory it keeps on hand, buying three additional warehouses to hold goods. “Everybody is loading up on inventory,” Mr. Greenspon said, “and prices for warehouses have spiked.”DPS Skis has had to overcome a kinked-up supply chain with steps like changing the source of the wood that goes into skis.Alex Goodlett for The New York TimesThe company’s production facilities are in Asia, so “the supply chain issue is something that dominates every conversation.” Mr. Greenspon said. He has explored moving production to Mexico or the United States — shortening the supply chain, as experts advise — but hasn’t been able to find a satisfactory supplier yet. “You can’t sell what you don’t have,” he said.Reshoring is a buzzword these days, but it’s premature to expect a domestic manufacturing renaissance as a result of the supply-chain mess, said Willy C. Shih, a professor at Harvard Business School. “We will bring things back, but it’s harder than you think,” he said.Understand the Supply Chain CrisisCard 1 of 5Covid’s impact on the supply chain continues. More